Hot-dip galvanizing protects steel or iron by covering it with a layer of zinc, preventing rust and damage. For over 150 years, hot dip galvanizing services have been trusted to safeguard metal from the elements. The process involves dunking metal into molten zinc, creating a durable shield. But how does this work? Why is it such an effective way to protect metal?
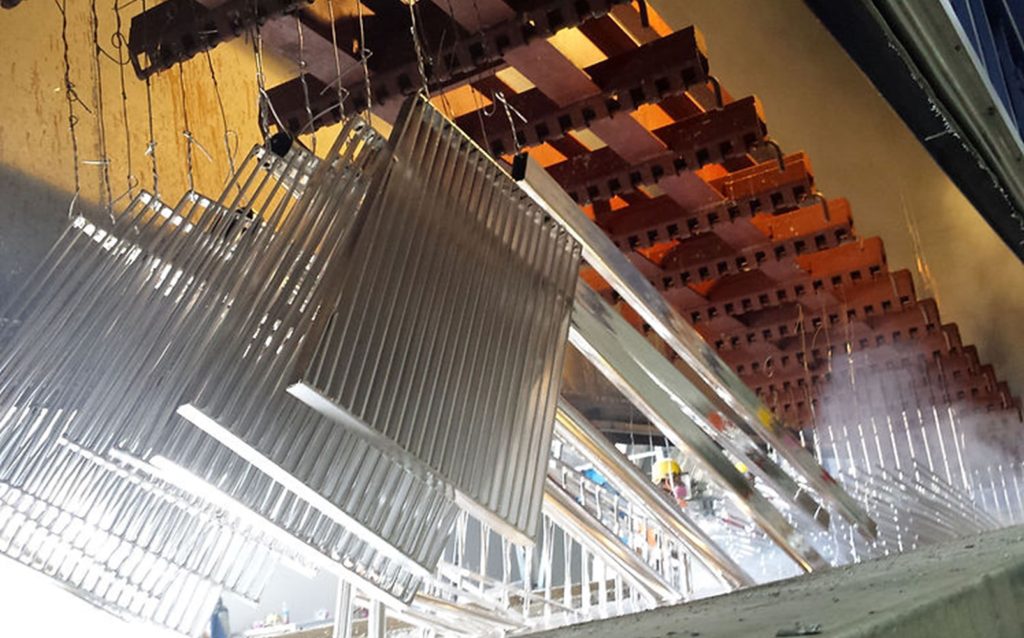
In this blog, we’ll explore what hot-dip galvanizing is, how it functions, and why it remains a popular method across various industries.
What Is Hot-Dip Galvanizing?
Hot-dip galvanizing, also known as HDG, covers steel or iron with zinc by dipping the metal into hot, liquid zinc. The zinc forms a tough shield that guards the metal against rust. This process creates a much stronger layer than paint or spray coatings. The result? Metal that stands firm against rust for a long time. HDG proves to be a perfect choice for bridges, pipes, and other important structures that need to last.
Why Is Zinc Used in Hot-Dip Galvanizing?
Zinc works best in this process because of its unique traits. Zinc sacrifices itself to protect the steel or iron. Even if the metal gets scratched, zinc will still keep it safe. Zinc will corrode before the steel or iron does, adding extra protection. Once zinc touches the air, it forms a layer that makes it even harder for rust to get in. This makes hot-dip galvanizing extremely durable, even in tough environments.
How Does the Hot-Dip Galvanizing Process Work?
Several steps make up the hot-dip galvanizing process. Each step ensures the steel or iron gets the best possible coating. Here’s a breakdown of how the process works:
1. Surface Preparation
Before dipping the metal into zinc, it must be squeaky clean. Dirt, oil, or rust can prevent zinc from sticking to the metal. Without proper cleaning, the zinc won’t bond. This step involves three main stages:
- Degreasing: The metal goes into a solution that scrubs off grease, dirt, and oils.
- Pickling: The metal is placed in a special acid bath that wipes away rust and scale.
- Fluxing: A chemical called flux coats the metal. It stops rust from returning and helps the zinc stick properly.
After cleaning, the metal is ready to be dipped in molten zinc.
2. Dipping the Metal in Molten Zinc
Next, the clean metal gets dipped into a bath of molten zinc. The zinc is heated to around 450°C (840°F). When the metal meets the hot zinc, the two react instantly. The zinc grabs hold of the metal, bonding with it to form layers of zinc-iron alloy. These layers anchor tightly to the surface. This creates a much stronger and longer-lasting shield compared to regular paint or other coatings.
3. Cooling and Inspection
After the dip, the metal cools down, and the zinc coating hardens. The cooling process locks the zinc in place, ensuring it sticks evenly around the metal. Once cool, the metal gets carefully checked to make sure it is fully covered with zinc. If the coating isn’t perfect, more zinc can be added.
Benefits of Hot-Dip Galvanizing
Hot-dip galvanizing brings many advantages compared to other methods of protecting steel and iron. Here’s why it remains a favorite for big projects.
1. Long-Lasting Protection
The zinc layer from hot-dip galvanizing can protect the metal for decades, sometimes as long as 50 years. This makes it ideal for structures exposed to rough weather, like bridges and fences.
2. Low Maintenance
Once the metal gets its zinc coating, it doesn’t need much attention. Even if the metal gets scratched or chipped, the zinc continues to protect it. This lowers the need for touch-ups or repairs.
3. Cost-Effective
Though hot-dip galvanizing may cost more upfront, the long-term benefits save money. Since it lasts so long and requires little upkeep, you’ll avoid extra costs for repairs or repainting.
4. Environmentally Friendly
Hot-dip galvanizing is also good for the environment. Zinc is a natural material that doesn’t release harmful chemicals. Plus, galvanized steel can be recycled. This makes it an eco-friendly way to protect metal.
Applications of Hot-Dip Galvanizing
Hot-dip galvanizing is used in many industries. Below are some of its most common uses.
- Construction: Beams, roofs, and columns are galvanized to prevent rust.
- Infrastructure: Bridges, railways, and utility poles benefit from galvanizing since they face harsh weather.
- Automotive: Car and truck parts are often made from galvanized steel to stop rust.
- Agriculture: Farm tools and fencing are exposed to the elements, so they need galvanized steel for protection.
- Energy and Utilities: Power poles and pipes rely on galvanizing to stand up against water, chemicals, and other damaging factors.
How to Choose a Hot-Dip Galvanizing Company
If you’re considering hot-dip galvanizing for your project, it’s important to pick the right company. The best hot-dip galvanizing company should have a lot of experience and follow industry standards closely. Choose a company that communicates well and explains the process in detail. They should have the proper tools to handle your project and provide quality work. Inspect their previous projects to make sure they consistently deliver high-quality results.
Conclusion
Hot-dip galvanizing protects steel and iron in an effective and lasting way. This process allows metal to withstand the harshest conditions, from rust to severe weather. By dipping the metal into molten zinc, hot-dip galvanizing creates a strong, long-lasting coating that can guard metal for decades.
Whether you’re working on a bridge, a fence, or a utility pole, hot-dip galvanizing ensures the structure stands the test of time. Not only does it provide excellent protection, but it also requires very little maintenance. This makes it an affordable and environmentally friendly option for projects that need reliable metal protection. For the best galvanizing services, VG Steel is your trusted partner. Our team ensures your steel gets the highest level of protection. Contact us today at 014-3624 014 or email us at vgironsales9@gmail.com to discuss your project needs. Protect your investment with VG Steel Industries!